Vibration Monitoring Services? What Are They, and Should You Use Them?
A vibration monitoring system is a complete system that is capable of receiving vibration signals based on specific parameters such as sampling frequency, vibration intensity, recording length, recording interval, and frequency bandwidth. The system should be able to process the sensor information and translate it so it can be interpreted intuitively by machine operators, upkeep personnel, or account managers. The system shouldn’t interrupt the operation of any machinery or structures being monitored, nor should it have a negative impact on the productivity or operation of the system.
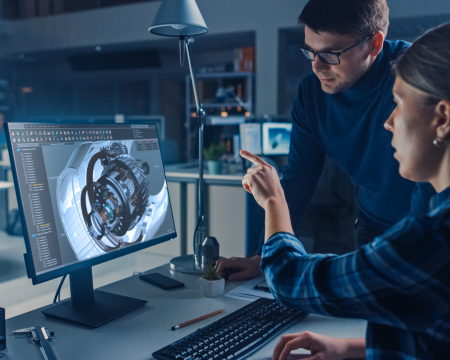
Nanoprecise Vibration Monitoring Services As the important components of machinery rotate, it gets more difficult to maintain tolerances, and the surface finish decreases performance. If problems are left long enough, breakdowns may also occur. Vibration monitoring services can keep you from losing money and downtime by having components checked prior to a breakdown.
Vibration monitoring is the process of using sensors to monitor changes in many kinds of machines and equipment sets. Increased levels of vibration may be an indicator of a developing malfunction, ruined process, or failure. Proper vibration monitoring for rotating machines is important to an effective and well-organized maintenance program. It can cut unscheduled downtime, improve maintenance, and minimize replacement and repair costs, thus enhancing a machine’s performance.
Types of Vibration Monitoring Methods You Won’t Know What to Do With!
vibration monitoring services are an essential part of any machine shop. By understanding the vibrations that are taking place in your device, you can improve its lifespan and performance. The most common types of vibrations are those caused by the moving parts of the equipment, such as gears and bearings. There are a number of ways to analyze these vibrations, but some of the most common methods used in this field are shocked pulse analysis (SPA), fast Fourier analysis (FFA), broadband vibration analysis (BVA), ultrasonic analysis (UA), and power spectral density (PSD). Each method has its own advantages and disadvantages.
Shock pulse analysis is one of the most common methods used to analyze vibrations. It is a simple process that involves sending a shockwave through your device in order to measure how it responds.
By analyzing vibrations, predicting repairs can be achieved.
Equipment like motors, pumps, and gearboxes frequently operate well at first but wear out as they age. A factory’s machinery relies on rotating parts, and dysfunction in these may necessitate repairs.
The shafts of equipment vibrate, the connections fail, and bearings wear as their friction increases. Inwardly, this type of damage is hardly discernible. At first, a gradual deterioration develops, becoming more pronounced as the equipment falls apart.
The evolution of any object’s vibrational dynamics can be traced back to changes in frequency, intensity, and amplitude, which can be used to identify a particular physical phenomenon. This ability to correlate vibration data to specific phenomena can allow engineers to use this data to perform particular analyses and adjust equipment to optimize performance.
Vibration monitoring services are oftentimes used in ongoing maintenance. It helps providers in preventing breakdowns and quality issues. These solutions support identifying recognizable vibration signals and subsequently predict when highly worn components will need replacement.
Partnering with a company like Nanoprecise Sci Corp, Inc. that specializes in Gearbox Vibration Monitoring can supply your plant the time and energy it needs to source the new parts it requires, plan for their installation, and maintain your manufacturing schedules, without needing to deal with the hassles of quality problems or being overdue with orders.
To get the most out of your vibration monitoring, you should seek it regularly.
Monitoring and fixing common issues is a possibility with vibration.
Vibration may lead to premature wear of equipment components, cause safety issues, shorten equipment life, and create noise. Misalignment and imbalance in rotating assets may break driveshafts and other parts.
Visually illustrating the severity of vibration.
A vibration monitor utilizes a color-coded hierarchy to alert maintenance teams of vibration intensity. The performance results of assets vary from preset baselines, causing the predictive maintenance software to sound an alarm if defined thresholds are exceeded.
Tracking asset health by measuring temperature and vibration.
Changes in the temperature of a surface may not precisely correlate to problems with the internal system, but changes in the ambient temperature that indicate the likelihood of consequent damage or faults can be a good heads-up for technicians.
What Exactly Is Gearbox Vibration Monitoring?
vibration analysis is a prevalent tool to monitor the operating condition of bearings and gears in transmission systems. This is due, in part, to their delicate nature and the need for precise tolerances. By using vibration analysis, owners can ensure that the bearing and gearbox are working as they should and improve machine accuracy. Additionally, vibration analysis can help identify potential problems with the transmission system before they become too severe.
Gear vibration monitoring is the evaluation or tracking of gear vibration.
Even though the gear teeth are not damaged, even a speedy little crack may induce a significant speed reduction in the apparatus. Furthermore, if the tooth is not adequately greased, friction also will be generated. Vibration analysis in gearboxes can help determine the impact of friction and its impact on predictive maintenance.
Monitoring vibration levels with specialized services.
An intricate vibration monitoring procedure goes far beyond simply obtaining a vibration analyzer. It calls for a strong practical knowledge of the software and tools used for vibration testing, plus an awareness of the engineering of rotating equipment.
If you would like to learn the best way to determine vibration in machine assemblies, then you will need to know more than just the fundamentals. This is where we are able to help. Our organization has nearly 20 years of experience providing automated vibration monitoring services that are designed to improve vibration analysis, no matter what your preferences are.
This method permits anyone with basic technical skills to make use of the sophisticated system while still providing an opportunity for those skills to perform intensive data interrogation.
conclusion
vibration monitoring services can help quantify the amount and type of vibration in gearboxes. This information can be used to improve the manufacturing process, create more accurate gears, or even steer a vehicle during a crash.