Predictive maintenance use cases
Nanoprecise Sci Corp strives to create a future of technology-enhanced efficiency through 360 degree integrated systems that bring prognostic and diagnostic data to our clients with unprecedented accuracy. Our cutting edge solutions aim to empower users to accurately predict the remaining useful life of any asset up to 99% accuracy – no matter what industry they’re in. Our mission is to revolutionize predictive maintenance, and ensure our clients are equipped with the right data to stay competitive and successful in a data-driven economy.
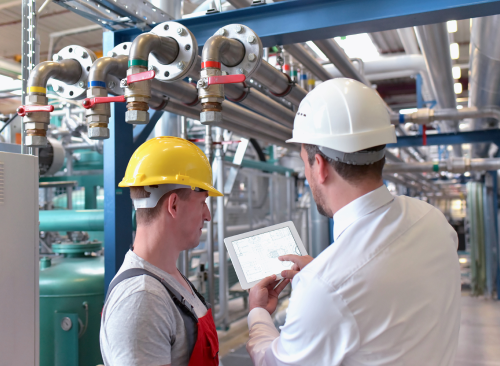
Predictive maintenance is a type of maintenance that uses predictions to make better decisions about when and how to repair or replace equipment. This type of maintenance is often used in manufacturing, where the need for accurate predictions can mean the difference between a unit meeting its production goals and one that doesn’t. Predictive maintenance can also be used in other industries, such as finance, where it can help optimize cash flow and manage risks.
What is predictive maintenance and why should it be used in the business?
Predictive maintenance in manufacturing is a process concerned with maintaining equipment and systems in a state that will allow for the efficient production of goods. It is used in factories to ensure that systems are functioning properly and to keep machines running safely. Predictive maintenance tells equipment operators what needs to be done in order for a certain system to operate optimally. When used correctly, predictive maintenance can help crews predict which repairs may need to be made and when they will have to be made so that the factory can stay productive. This way, workers can plan their work around the clock so that they can get the most out of their time at work.
Purpose: What are some typical uses of predictive maintenance in the business?
Predictive maintenance is a term that refers to the use of technology in order to improve the performance of equipment and systems. Predictive maintenance is used in manufacturing in order to ensure that systems run without fail, which results in increased efficiency andDecreased waste. Predictive maintenance can be used on a wide range of equipment, from machines to vehicles. In Manufacturing, predictive maintenance helps to ensure that systems run smoothly by predicting potential problems and correcting them accordingly. Some typical uses of predictive maintenance include: machine monitoring, elevator status, air pressure monitoring, and more. Machine monitoring helps manufacturers to track the performance of their machines over time and make better decisions about how to keep them running smoothly. Elevator status can help managers keep an eye on the health of their lifts so that they don’t have to spend time inspecting each one individually.
Types of predictability:
There are three main types of predictability, historical, present, and future.
Historical predictability is when something that has happened in the past is used to predict future events. A good example of this would be predicting the current state of a market.present predictability is when things are happening right now and can be used to make predictions about what will happen in the future. For example, you could say that the stock market will go up or down based on the present situation. Future predictability refers to predicting future events based on current trends or conditions. This can include things like forecasting economic indicators such as interest rates or stock prices.Once again, a good example of this would be predicting whether or not a market will crash over time.
Basic principles: How do predictive maintenance algorithms work and what are some common results?
Predictive maintenance algorithms are designed to provide early warning of potential problems in a system. In many cases, this information can be used to either fix the issue or prevent it from happening in the future. predictive maintenance algorithms are common in manufacturing, and can help to keep systems running smoothly and efficiently. Some common results of using predictive maintenance algorithms include improved performance and reduced downtime.
Prerequisites: What are some basic concepts about computers and data management?
There are a number of key concepts that are important when it comes to predictive maintenance in manufacturing. Predictive maintenance is a process that helps keep machines and parts running correctly, without causing downtime. This can be done through automated predictions of needed repairs, or through human predictions of whether a certain part will need to be replaced.
The two most common types of predictive maintenance are fault detection and correction. Fault detection uses data from the machines to predict where and when problems may happen. Correction uses software to fix errors or problems in the machines so that they run correctly.
A number of other factors must also be considered when predicting maintenance needs. These include the type of machine being used, how often it will be used, the equipment involved, and the environment in which it will be used.
Conclusion:
Nanoprecise Predictive maintenance is a valuable tool that can be used in a variety of ways to ensure the continued operability of systems. By understanding how and when to use predictive maintenance, system operators can keep their systems running smoothly and efficiently.